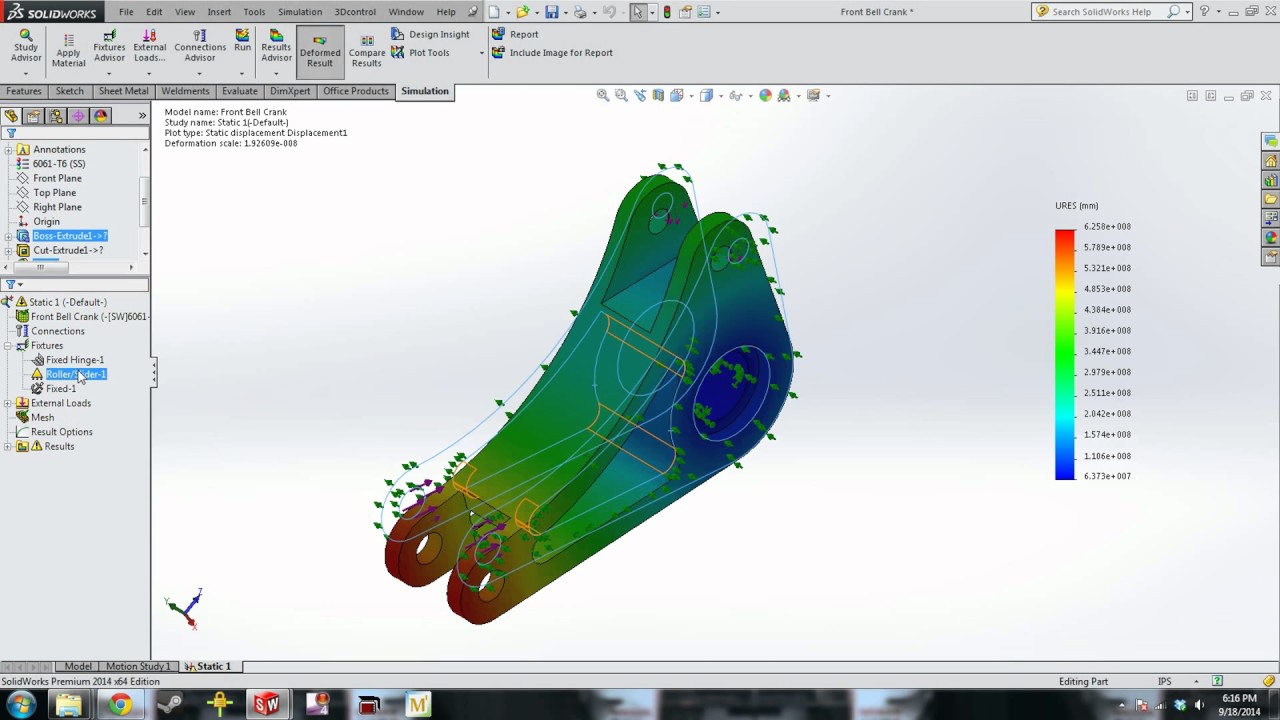
Finite Element Analysis (FEA) stands as a cornerstone of modern engineering, empowering designers and engineers to simulate and analyze the structural behavior of complex components, assemblies, and systems with unparalleled accuracy and precision. In this extensive exploration, we embark on a journey through the intricacies of Finite Element Analysis (FEA) in SolidWorks, unraveling its functionalities, benefits, and practical applications across diverse engineering disciplines.
Understanding Finite Element Analysis (FEA):
Finite Element Analysis (FEA) in SolidWorks entails the numerical simulation of structural behavior using the finite element method, a computational technique for approximating solutions to partial differential equations governing physical phenomena. By discretizing complex geometries into finite elements, FEA enables designers to analyze stress, strain, deformation, and other mechanical properties under various loading conditions, providing insights into performance, reliability, and safety considerations.
At its core, FEA serves as a virtual testing ground, allowing designers to predict and evaluate the response of structures to mechanical loads, thermal gradients, fluid flow, and other environmental factors. By simulating real-world conditions and scenarios, SolidWorks empowers designers to optimize designs, validate performance requirements, and mitigate potential issues early in the design process, ultimately enhancing product quality and reducing time-to-market.
Key Concepts of Finite Element Analysis (FEA) in SolidWorks:
- Model Preparation and Meshing: FEA in SolidWorks begins with model preparation and meshing, where designers define the geometry, material properties, boundary conditions, and loads of the structure under analysis. SolidWorks automates the meshing process, dividing the geometry into finite elements and nodes, ensuring accuracy, convergence, and computational efficiency in the simulation.
- Material Properties and Behavior: SolidWorks provides a comprehensive library of material properties for FEA simulations, including linear and nonlinear materials, isotropic and anisotropic materials, and hyperelastic materials. Designers can assign material properties such as modulus of elasticity, Poisson’s ratio, and yield strength to accurately represent material behavior under loading conditions.
- Analysis Types and Solvers: SolidWorks supports various analysis types and solvers for FEA simulations, including static analysis, dynamic analysis, thermal analysis, fatigue analysis, and nonlinear analysis. Designers can choose appropriate analysis types based on the nature of the problem and the desired outcomes, leveraging advanced solver algorithms to compute stress, displacement, and other mechanical properties.
- Results Visualization and Interpretation: FEA in SolidWorks includes tools for visualizing and interpreting simulation results, allowing designers to analyze stress contours, displacement plots, deformation animations, and other mechanical responses. Designers can assess factors such as safety factors, factor of safety, and failure criteria, gaining insights into design performance and behavior under different loading conditions.
Benefits of Finite Element Analysis (FEA) in SolidWorks:
- Performance Optimization: FEA enables designers to optimize the performance of structures by evaluating and refining designs based on simulation results. By identifying potential issues such as stress concentrations, excessive deformation, and material failure, designers can iteratively improve designs, enhancing performance, reliability, and durability.
- Design Validation: SolidWorks facilitates design validation through FEA simulations, allowing designers to verify that structures meet performance requirements and specifications. By comparing simulation results against design criteria, standards, and regulations, designers can ensure that designs are safe, compliant, and fit for purpose.
- Risk Mitigation: FEA helps mitigate risk by identifying and addressing potential issues and failure modes early in the design process. By simulating extreme loading conditions, evaluating safety factors, and predicting failure modes, designers can anticipate and mitigate risks such as structural failure, deformation, and fatigue, reducing the likelihood of costly errors and recalls.
- Cost and Time Savings: FEA in SolidWorks streamlines the design process and reduces time-to-market by enabling designers to conduct virtual testing and optimization within the same integrated environment as CAD modeling. By eliminating the need for physical prototypes and empirical testing, designers can iterate on designs rapidly, identify design flaws early, and bring products to market faster and more cost-effectively.
Practical Applications of Finite Element Analysis (FEA) in SolidWorks:
- Structural Engineering: FEA in SolidWorks is widely used in structural engineering for analyzing and designing buildings, bridges, and other civil structures. Engineers leverage FEA to assess structural integrity, evaluate load-bearing capacity, and optimize structural configurations to withstand static and dynamic loading conditions.
- Mechanical Design: SolidWorks supports mechanical design applications through FEA simulations, enabling designers to analyze and optimize the performance of machine components, mechanisms, and assemblies. Designers leverage FEA to evaluate stress concentrations, deflection, and fatigue life, ensuring that designs meet performance requirements and reliability standards.
- Product Development: FEA plays a critical role in product development for simulating and testing the structural behavior of consumer products, industrial equipment, and automotive components. Designers use FEA to assess product durability, evaluate crashworthiness, and optimize designs for weight reduction, performance enhancement, and cost efficiency.
- Aerospace and Defense: SolidWorks facilitates aerospace and defense applications through FEA simulations, enabling engineers to analyze and optimize the performance of aircraft structures, spacecraft components, and defense systems. Engineers leverage FEA to evaluate structural integrity, assess fatigue life, and optimize designs for weight savings, aerodynamic efficiency, and mission requirements.
Conclusion:
Finite Element Analysis (FEA) in SolidWorks represents a powerful tool for simulating and analyzing the structural behavior of complex systems with unparalleled accuracy and precision. By leveraging advanced simulation capabilities, designers and engineers can optimize designs, validate performance requirements, and mitigate risks early in the design process, ultimately enhancing product quality, reliability, and competitiveness in the market. Whether used for structural engineering, mechanical design, product development, or aerospace applications, FEA empowers designers to master complexity, ensure safety, and drive innovation in engineering and manufacturing.