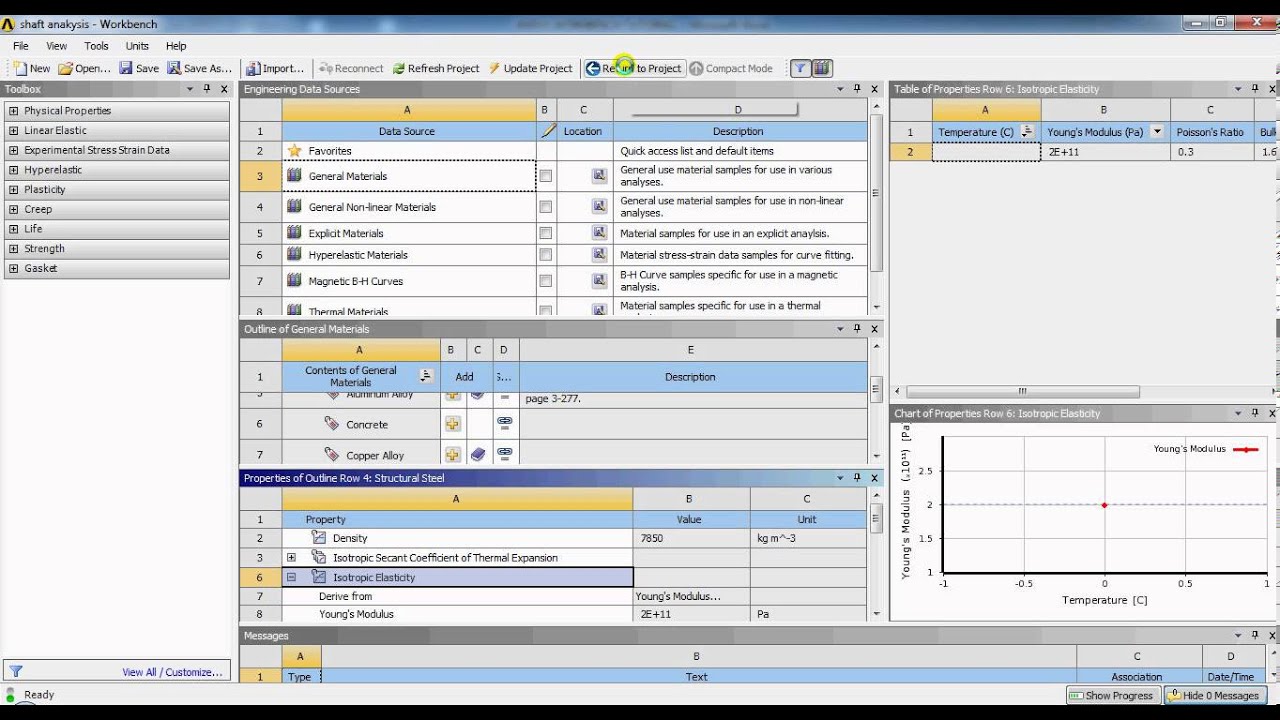
Defining material properties accurately is crucial for performing reliable simulations and analyses using ANSYS software across various engineering disciplines. ANSYS offers a comprehensive suite of tools and capabilities to model a wide range of material behaviors, from isotropic materials to complex anisotropic materials with nonlinear characteristics. This guide will walk you through the step-by-step process of defining material properties in ANSYS, covering basic material definitions, advanced material models, considerations for specific applications, and best practices.
Table of Contents
- Introduction to Material Properties in ANSYS
- Basic Material Property Definitions
- Advanced Material Models in ANSYS
- Defining Material Properties for Specific Applications
- Best Practices for Defining Material Properties
- Troubleshooting Material Property Issues
- Conclusion
1. Introduction to Material Properties in ANSYS
Material properties define how materials respond to various physical phenomena such as mechanical loading, thermal effects, electromagnetic fields, and more. ANSYS provides a robust framework for specifying material properties accurately, enabling engineers to simulate real-world conditions and predict material behavior under different operating conditions.
2. Basic Material Property Definitions
- Elastic Modulus (Young’s Modulus):
- Defines the stiffness of the material under linear elastic deformation.
- Represents the ratio of stress to strain in the linear elastic region.
- Poisson’s Ratio:
- Specifies the ratio of transverse strain to longitudinal strain in a material under uniaxial loading.
- Indicates how the material deforms laterally when subjected to axial stress.
- Density:
- Represents the mass per unit volume of the material.
- Affects dynamic analyses and simulations involving inertial effects.
- Thermal Conductivity:
- Defines the ability of the material to conduct heat.
- Critical for thermal analyses to simulate heat transfer through materials.
- Specific Heat Capacity:
- Indicates the amount of heat required to raise the temperature of the material by one degree.
- Important for transient thermal analyses and heat transfer simulations.
3. Advanced Material Models in ANSYS
- Nonlinear Material Behavior:
- Define nonlinear stress-strain relationships for materials exhibiting plasticity, hyperelasticity, or viscoelasticity.
- Use material models such as Von Mises plasticity, Drucker-Prager plasticity, Mooney-Rivlin hyperelasticity, and more.
- Creep and Fatigue:
- Model time-dependent material deformation under constant load (creep) or cyclic loading (fatigue).
- Specify creep and fatigue properties including creep strain rate, fatigue life, and stress-life curves.
- Anisotropic Materials:
- Define material properties that vary with direction due to material symmetry or fiber orientation.
- Specify directional elastic constants (orthotropic materials) or more complex anisotropic models.
- Temperature-Dependent Properties:
- Incorporate temperature dependency into material models by defining temperature-dependent material properties.
- Use temperature curves or functions to specify variations in material properties with temperature.
4. Defining Material Properties for Specific Applications
- Structural Mechanics:
- Define material properties for structural analyses including static, dynamic, and nonlinear analyses.
- Consider material nonlinearity, plasticity, and failure criteria for accurate structural simulations.
- Thermal Analyses:
- Specify thermal conductivity, specific heat, and thermal expansion coefficients for thermal simulations.
- Include temperature-dependent properties for accurate thermal analysis predictions.
- Fluid Dynamics:
- Define fluid properties such as density, viscosity, and specific heat for fluid flow simulations using ANSYS Fluent.
- Model fluid behavior under varying flow conditions and environmental factors.
- Electromagnetics:
- Define electrical conductivity, relative permittivity, magnetic permeability, and other electromagnetic properties.
- Simulate electromagnetic fields and interactions with materials accurately.
5. Best Practices for Defining Material Properties
- Use Experimental Data:
- Base material properties on experimental test data whenever possible to ensure accuracy and reliability.
- Validate material models against experimental results to calibrate simulation predictions.
- Understand Material Behavior:
- Gain knowledge of material characteristics and behavior under different loading conditions (e.g., tension, compression, shear).
- Consult material datasheets, handbooks, or research publications for detailed material information.
- Consider Environmental Factors:
- Account for environmental conditions (temperature, humidity, radiation) that may affect material properties.
- Incorporate temperature dependencies and environmental effects into material models as needed.
- Validate and Verify:
- Perform sensitivity analyses and validation studies to assess the impact of material properties on simulation results.
- Verify simulation predictions against benchmark cases or physical tests to ensure accuracy and reliability.
6. Troubleshooting Material Property Issues
- Model Convergence Issues:
- Address convergence problems by refining mesh resolution, adjusting solver settings, or modifying material models.
- Ensure numerical stability and solution convergence in nonlinear analyses.
- Incorrect Property Assignment:
- Double-check material property assignments to ensure correct definitions and units.
- Verify material assignments at component or assembly levels to avoid inconsistencies.
- Compatibility and Interoperability:
- Verify compatibility between ANSYS versions and CAD software for seamless material property transfer.
- Convert CAD files to supported formats if issues arise during geometry import and material assignment.
7. Conclusion
Defining material properties accurately in ANSYS is essential for achieving reliable simulation results across a wide range of engineering applications. By following the guidelines and best practices outlined in this guide, engineers and analysts can effectively specify material properties, choose appropriate material models, and simulate realistic material behavior under various conditions using ANSYS software. Understanding the nuances of material property definitions, advanced material models, and application-specific considerations empowers users to conduct robust simulations, optimize designs, and make informed engineering decisions to drive innovation and ensure product performance and reliability. ANSYS’s comprehensive capabilities for material modeling and simulation support diverse industries in tackling complex engineering challenges with confidence and precision.