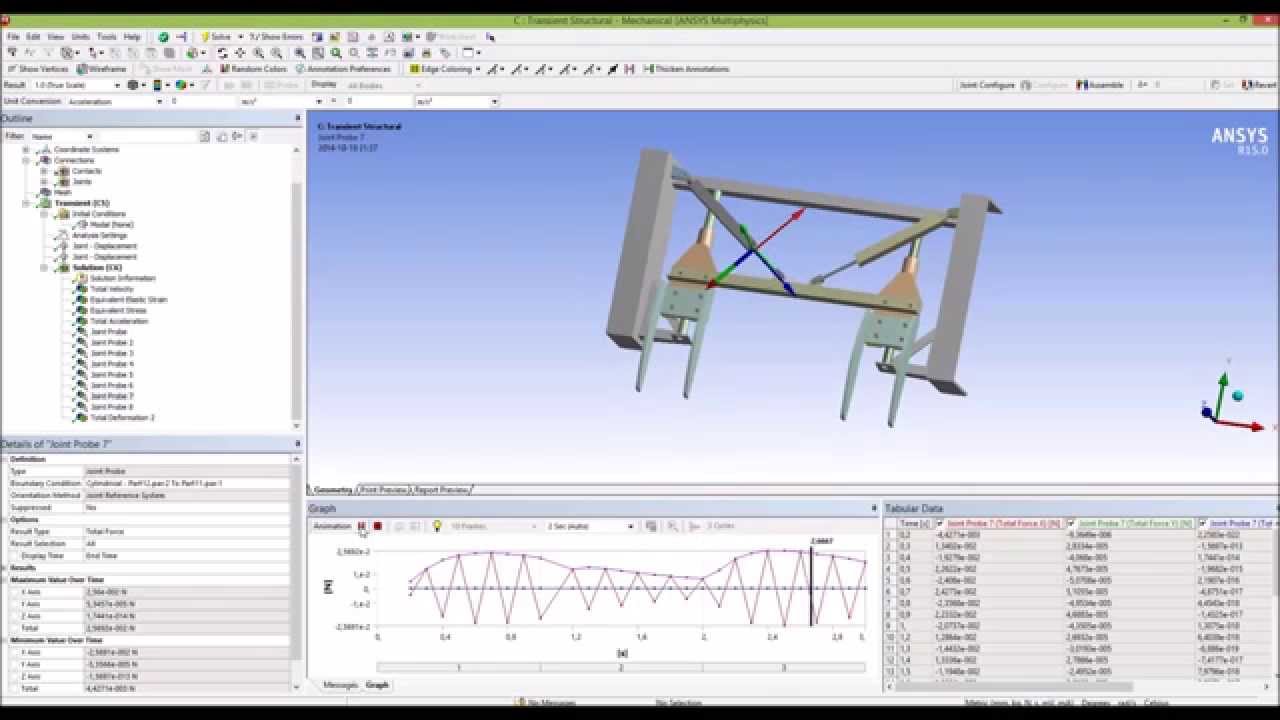
Running a transient structural analysis in ANSYS involves simulating how a structure responds over time to dynamic loading, such as varying forces, thermal effects, or mechanical impacts. This type of analysis is crucial for understanding the time-dependent behavior of components and systems subjected to transient conditions, which are common in real-world engineering applications. This comprehensive guide will walk you through the step-by-step process of setting up and running a transient structural analysis in ANSYS, covering theory, pre-processing, solution setup, post-processing, and interpretation of results.
Table of Contents
- Introduction to Transient Structural Analysis
- Preparing Geometry for Transient Structural Analysis
- Setting Up Transient Structural Analysis in ANSYS
- Defining Time-Dependent Loads and Boundary Conditions
- Solving the Transient Structural Analysis
- Post-Processing and Analyzing Results
- Advanced Techniques and Considerations
- Troubleshooting and Common Issues
- Conclusion
1. Introduction to Transient Structural Analysis
Transient structural analysis in ANSYS focuses on studying how structures deform and respond to time-varying loads and boundary conditions. Unlike static analyses that assume steady-state conditions, transient analyses capture dynamic effects such as vibrations, impacts, thermal transients, and transient fluid-structure interactions. This capability is essential for designing structures to withstand dynamic loading conditions and predicting fatigue life, durability, and safety margins accurately.
2. Preparing Geometry for Transient Structural Analysis
- Import CAD Geometry:
- Start by importing the CAD geometry of the structure or component into ANSYS.
- Supported formats include STEP, IGES, Parasolid, and native CAD formats.
- Geometry Cleanup and Simplification:
- Ensure the geometry is clean and free from any gaps, overlaps, or small features that may affect mesh quality and analysis results.
- Simplify complex geometries to optimize computational resources and improve mesh quality.
- Mesh Generation:
- Generate a finite element mesh on the geometry using ANSYS Meshing or TGrid.
- Ensure the mesh is refined enough to capture critical details and features of the structure.
3. Setting Up Transient Structural Analysis in ANSYS
- Launch ANSYS Workbench:
- Start ANSYS Workbench and create a new project for structural analysis.
- Physics Settings:
- Select the “Transient Structural” module under ANSYS Mechanical for transient analysis.
- Define material properties, such as elastic modulus, Poisson’s ratio, density, and thermal properties if applicable.
- Solver Settings:
- Configure solver settings for transient analysis, including time step size, total time duration, and convergence criteria.
- Choose appropriate solver options based on the dynamics of the problem (implicit or explicit dynamics).
4. Defining Time-Dependent Loads and Boundary Conditions
- Time-Dependent Loads:
- Specify loads that vary with time, such as varying forces, displacements, thermal profiles, or pressure distributions.
- Define load functions or profiles to describe the time dependency of applied loads accurately.
- Boundary Conditions:
- Define time-dependent boundary conditions such as prescribed displacements, velocities, thermal profiles, or contact interactions.
- Ensure boundary conditions reflect the dynamic nature of the problem and operational scenarios.
5. Solving the Transient Structural Analysis
- Mesh Check and Validation:
- Verify mesh quality and element aspect ratios to ensure numerical stability and solution accuracy.
- Address any mesh quality issues through refinement or smoothing techniques.
- Solver Execution:
- Launch the solver to perform the transient structural analysis.
- Monitor solver progress and convergence status to ensure the analysis completes successfully.
- Time Step Adjustment:
- Adjust the time step size iteratively based on solver feedback and simulation results.
- Balance between computational efficiency and solution accuracy by refining time steps in critical phases.
6. Post-Processing and Analyzing Results
- Time History Data:
- Extract and analyze time-dependent results such as displacements, stresses, strains, and velocities over the simulation duration.
- Plot time histories to visualize how structural responses evolve over time under varying loading conditions.
- Transient Response Analysis:
- Evaluate dynamic characteristics such as natural frequencies, mode shapes, damping ratios, and transient responses.
- Identify critical time intervals or events affecting structural integrity or performance.
- Fatigue and Durability Analysis:
- Perform fatigue analysis to assess potential fatigue life and durability under repeated dynamic loading conditions.
- Predict fatigue failure modes and fatigue-induced damage accumulation.
7. Advanced Techniques and Considerations
- Transient Fluid-Structure Interaction (FSI):
- Model interactions between fluids and structures using coupled simulations (e.g., ANSYS Mechanical and Fluent).
- Analyze dynamic responses of structures subjected to fluid-induced forces and pressures.
- Impact and Drop Testing:
- Simulate impact and drop tests to evaluate structural responses to sudden loading or collision events.
- Study impact dynamics, energy absorption, and stress distributions during impact scenarios.
- Nonlinear Transient Analysis:
- Incorporate nonlinear material behaviors, large deformations, and contact interactions in transient analyses.
- Use advanced material models (e.g., plasticity, hyperelasticity) to capture nonlinear effects accurately.
8. Troubleshooting and Common Issues
- Convergence Problems:
- Address convergence issues by refining mesh, adjusting time step size, or modifying solver settings.
- Ensure numerical stability and convergence throughout the transient analysis.
- Inaccurate Results:
- Verify boundary conditions, material properties, and load definitions for accuracy and consistency.
- Check for modeling assumptions and simplifications that may affect simulation fidelity.
- Computational Resources:
- Optimize computational resources by balancing mesh refinement with solver efficiency.
- Use parallel processing and distributed computing options for large-scale transient analyses.
9. Conclusion
Running a transient structural analysis in ANSYS enables engineers to simulate and analyze the dynamic behavior of structures under time-varying conditions accurately. By following the comprehensive steps and guidelines outlined in this guide, engineers can effectively set up, execute, and interpret transient structural simulations using ANSYS. Understanding the nuances of transient analysis, from geometry preparation to post-processing of results, empowers engineers to predict dynamic responses, optimize designs, and ensure structural reliability and performance across various engineering applications. ANSYS’s powerful capabilities in transient analysis support innovation and engineering excellence, enabling engineers to tackle complex dynamic problems with confidence and precision.