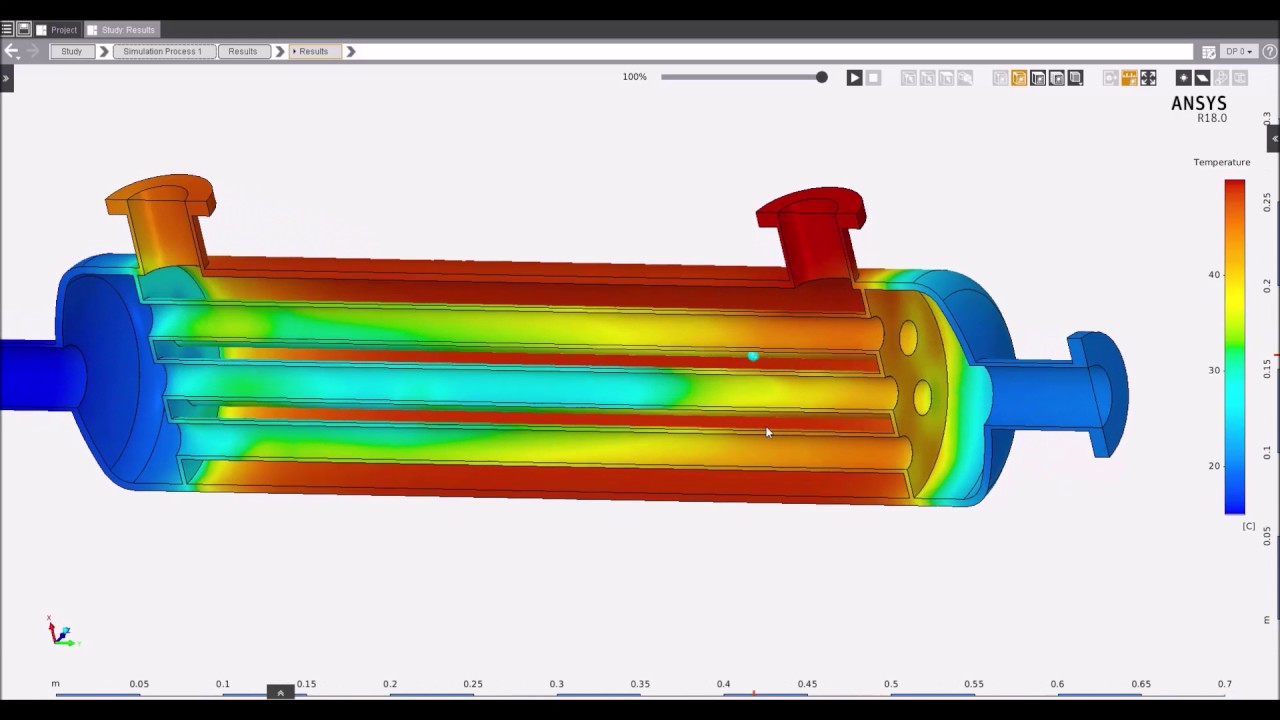
To conduct comprehensive multi-physics simulations effectively, ANSYS Workbench provides a powerful platform that integrates various physics disciplines such as structural mechanics, fluid dynamics, electromagnetics, and thermal analysis. This guide will walk you through the step-by-step process of using ANSYS Workbench for multi-physics simulations, covering the fundamentals, setup procedures, workflow integration, advanced techniques, and best practices.
Table of Contents
- Introduction to Multi-Physics Simulations in ANSYS Workbench
- Overview of ANSYS Workbench Environment
- Setting Up Multi-Physics Simulations
- Defining Coupling and Interaction Between Physics Domains
- Solving Multi-Physics Simulations
- Post-Processing and Analyzing Results
- Advanced Techniques and Considerations
- Best Practices for Multi-Physics Simulations
- Troubleshooting Common Issues
- Conclusion
1. Introduction to Multi-Physics Simulations in ANSYS Workbench
Multi-physics simulations involve analyzing interactions between different physical phenomena within a single simulation environment. ANSYS Workbench facilitates the integration of structural, fluid, thermal, electromagnetic, and other physics domains to simulate real-world behavior accurately. Applications range from designing complex systems to optimizing performance and predicting behavior under coupled physical effects.
2. Overview of ANSYS Workbench Environment
- Project Schematic:
- ANSYS Workbench uses a project-based approach, where simulations are organized into a project schematic.
- Modules such as Mechanical, Fluent, Maxwell, and more can be added to the project for specific physics simulations.
- Engineering Data Management:
- Workbench manages geometry, meshing, material properties, boundary conditions, and results within a unified interface.
- Provides tools for geometry import, CAD interaction, mesh generation, and post-processing of results.
- Integration and Workflow:
- Physics modules in Workbench are integrated to share geometry, mesh, and results seamlessly.
- Workflow automation and parameterization streamline iterative design studies and optimization processes.
3. Setting Up Multi-Physics Simulations
- Create New Project:
- Launch ANSYS Workbench and create a new project for multi-physics simulations.
- Define project settings, units, and analysis type (e.g., static, transient, harmonic).
- Add Physics Modules:
- Select appropriate physics modules (Mechanical, Fluent, Maxwell, etc.) based on the types of physics interactions involved.
- Configure each module for specific physics domains, such as structural mechanics, fluid dynamics, electromagnetics, or thermal analysis.
- Geometry Preparation:
- Import CAD geometry into Workbench or create geometry directly using DesignModeler or SpaceClaim.
- Ensure geometry is clean and suitable for multi-physics simulations, considering interfaces and interaction regions.
4. Defining Coupling and Interaction Between Physics Domains
- Coupling Interfaces:
- Define coupling interfaces between different physics modules to exchange data and interact physically.
- Specify coupling conditions such as displacement-temperature coupling, thermal-fluid coupling, or electromagnetic-structural coupling.
- Boundary Conditions:
- Define boundary conditions for each physics domain independently based on simulation requirements.
- Ensure consistency and compatibility of boundary conditions across coupled domains.
- Material Properties:
- Assign material properties relevant to each physics domain (e.g., elasticity, conductivity, viscosity) within respective modules.
- Verify material definitions and properties to accurately represent physical behavior.
5. Solving Multi-Physics Simulations
- Solver Configuration:
- Configure solver settings for each physics module considering coupling effects and convergence requirements.
- Adjust time steps, iteration controls, and solver tolerances based on simulation dynamics and accuracy goals.
- Parallel Processing:
- Utilize parallel processing capabilities to enhance computational efficiency for large-scale multi-physics simulations.
- Distribute computational load across multiple cores or processors to expedite solution times.
- Solution Monitoring:
- Monitor solver progress and convergence status during multi-physics simulations.
- Review solver diagnostics, error messages, and warnings to troubleshoot issues promptly.
6. Post-Processing and Analyzing Results
- Multi-Physics Results Integration:
- Integrate and visualize results from different physics modules within Workbench.
- Overlay field data, plot contours, and compare simulations to analyze coupled effects and interactions.
- Performance Metrics:
- Evaluate performance metrics such as stresses, displacements, temperatures, velocities, electromagnetic fields, and fluid flow parameters.
- Extract key performance indicators (KPIs) to assess system behavior under multi-physics conditions.
- Design Optimization:
- Use simulation results to optimize design parameters and improve system performance across integrated physics domains.
- Conduct sensitivity analyses and parametric studies to explore design variations and validate performance improvements.
7. Advanced Techniques and Considerations
- Transient Multi-Physics Simulations:
- Perform transient analyses to study time-dependent behavior and dynamic interactions between coupled physics domains.
- Address transient effects such as fluid-structure interaction, thermal-electromagnetic coupling, and more.
- Nonlinear Multi-Physics Analysis:
- Incorporate nonlinear material behavior, large deformations, and complex interactions in multi-physics simulations.
- Use advanced material models, contact formulations, and multiphase flow models as needed.
- Electromagnetic-Thermal Coupling:
- Analyze thermal effects induced by electromagnetic fields and vice versa.
- Study Joule heating, thermal dissipation, and electromagnetic losses in integrated thermal-electromagnetic simulations.
8. Best Practices for Multi-Physics Simulations
- Model Validation:
- Validate multi-physics models against experimental data, analytical solutions, or benchmark cases.
- Ensure accuracy and reliability of simulation predictions across coupled physics domains.
- Iterative Design Process:
- Adopt an iterative design approach using Workbench’s parametric capabilities and optimization tools.
- Iterate design modifications based on simulation feedback to achieve performance targets and design goals.
- Documentation and Collaboration:
- Document simulation setups, methodologies, and results comprehensively for reproducibility and knowledge sharing.
- Collaborate with interdisciplinary teams to leverage expertise and insights for multi-physics simulation projects.
9. Troubleshooting Common Issues
- Convergence Challenges:
- Address convergence issues by refining mesh resolution, adjusting solver settings, or enhancing numerical methods.
- Monitor convergence criteria and solution stability during iterative simulations.
- Interface Compatibility:
- Verify compatibility and consistency of coupling interfaces between different physics modules.
- Ensure proper data exchange and physical interaction representation across coupled domains.
- Resource Management:
- Optimize computational resources by balancing mesh refinement, solver parallelization, and memory allocation.
- Manage disk space, temporary files, and system resources for efficient multi-physics simulations.
10. Conclusion
ANSYS Workbench provides a versatile platform for conducting multi-physics simulations, enabling engineers and researchers to analyze complex systems with integrated physics interactions effectively. By following the comprehensive steps, guidelines, and best practices outlined in this guide, users can leverage ANSYS Workbench’s capabilities to simulate, optimize, and validate designs across diverse engineering applications. Mastering multi-physics simulations enhances innovation, accelerates product development, and enables informed decision-making in designing advanced systems and components. ANSYS’s integrated approach to multi-physics simulation supports engineering excellence by addressing real-world challenges with accuracy, efficiency, and reliability.