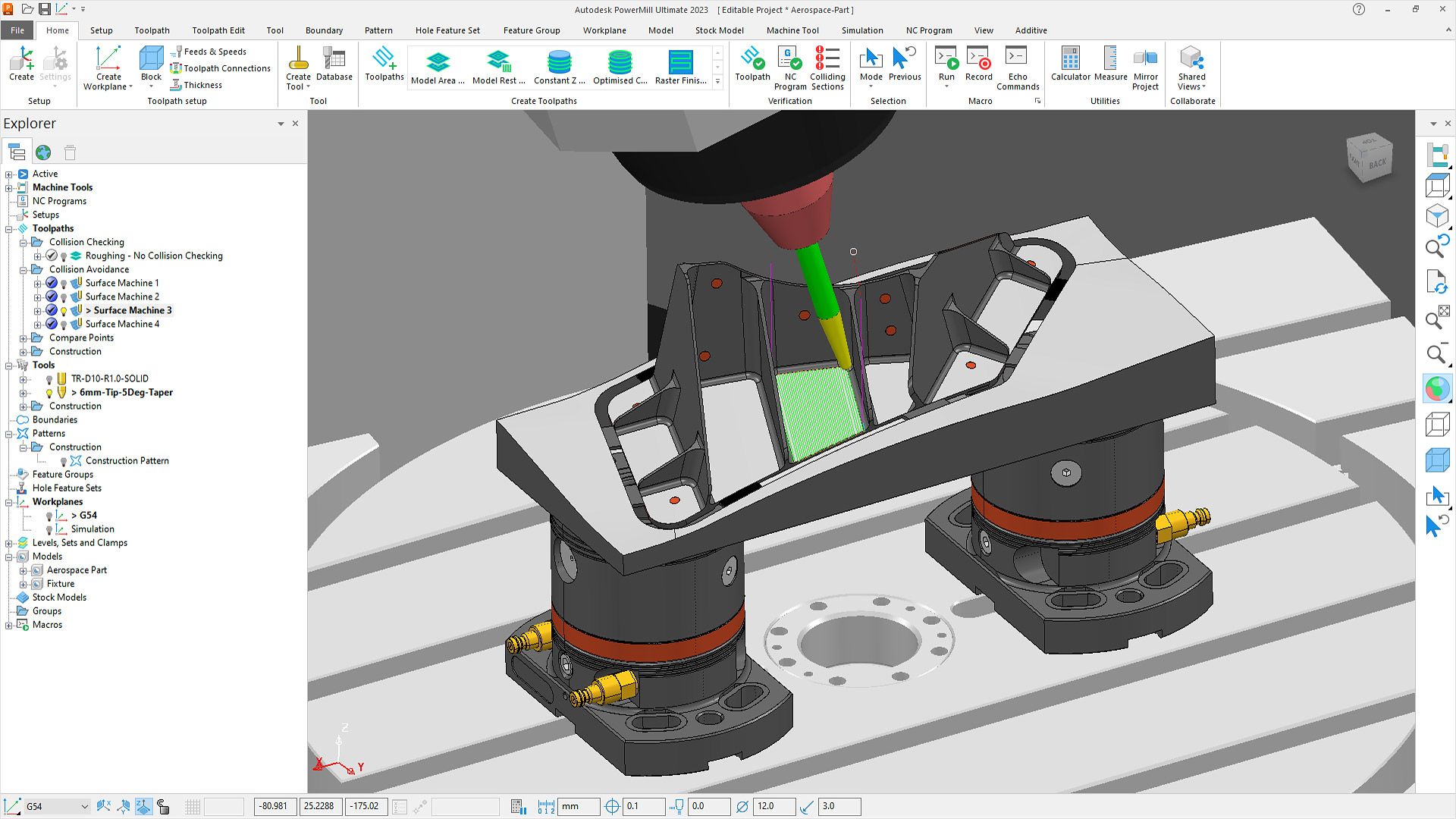
PowerMill Ultimate, a crown jewel in the Autodesk portfolio, stands as a titan of Computer-Aided Manufacturing (CAM) software. Its prowess lies in generating optimized toolpaths for complex 5-axis machining, breathing life into intricate designs. But PowerMill isn’t meant to operate in isolation. To unlock its full potential, seamless integration with other software is crucial. This article delves deep into the world of PowerMill Ultimate integration, exploring various avenues to connect it with the programs that fuel your design and manufacturing workflow.
The Power of CAD: Design as the Foundation
PowerMill thrives on a solid design foundation. Integration with Computer-Aided Design (CAD) software is paramount. Here’s a look at some key players:
-
Autodesk Fusion 360: This dream team combines the strengths of both worlds. Fusion 360, with its robust design capabilities, integrates flawlessly with PowerMill Ultimate. This eliminates data loss from file format conversions and ensures a smooth transition from design to manufacturing. Imagine sketching your concept in Fusion 360, utilizing its powerful free-form modeling tools, and then seamlessly pushing it to PowerMill for expert toolpath generation – a true one-stop shop for design and manufacturing.
-
SOLIDWORKS: As another popular CAD platform, SOLIDWORKS can integrate with PowerMill through HSMWorks. This add-on brings CAM functionalities directly within the SOLIDWORKS interface. Designers can leverage the power of PowerMill’s toolpath generation without leaving their familiar SOLIDWORKS environment. This streamlines the workflow and reduces the need for data transfer between programs.
-
Third-Party CAD Solutions: PowerMill boasts the ability to work with various CAD file formats, including IGES, STEP, and Parasolid. This allows for broader integration with other CAD software beyond the Autodesk ecosystem. While some level of data translation might be involved, PowerMill can still effectively utilize the design data for toolpath creation.
CAM Colleagues: Collaboration for Efficiency
Beyond design, PowerMill can integrate with other CAM software for specific functionalities:
-
Mastercam: While competitors in the CAM arena, PowerMill and Mastercam can coexist. Through translators or neutral file formats, toolpath data can be exchanged between the two. This allows for leveraging the strengths of each program for specific tasks. Perhaps a complex 5-axis machining project is best suited for PowerMill, while 2.5D milling might be handled more efficiently in Mastercam.
-
Custom Programming and Scripting: Advanced users can leverage PowerMill’s Application Programming Interface (API) to create custom scripts and programs. This allows for integration with other CAM software or in-house manufacturing management systems. Imagine an automated script that pulls design data from a central repository, generates toolpaths in PowerMill, and then sends them directly to the CNC machine controller – a powerful solution for high-volume production.
Beyond Design and CAM: The Manufacturing Ecosystem
PowerMill plays a vital role in the bigger picture of manufacturing. Here’s how it connects with other crucial software:
-
Computer-Aided Engineering (CAE): Software like ANSYS allows for virtual simulation of machining processes. By integrating PowerMill’s generated toolpaths with CAE software, manufacturers can virtually test their machining strategies, identify potential issues like collisions or excessive tool stress, and refine the toolpaths before committing to physical production. This leads to a more efficient and optimized manufacturing process.
-
Manufacturing Execution Systems (MES): MES software manages and monitors the entire production process. PowerMill can integrate with MES systems to provide real-time toolpath data, enabling production planning, scheduling, and tracking. This improves visibility and control over the manufacturing floor, allowing for better resource allocation and production optimization.
-
CNC Machine Controllers: Ultimately, PowerMill’s toolpaths need to be understood by the CNC machine controller that will execute them. PowerMill offers a wide range of post-processors, which translate the toolpath data into the specific language understood by each CNC machine controller. Choosing the right post-processor ensures accurate and efficient communication between PowerMill and the CNC machine.
Strategies for Successful Integration
While the possibilities for PowerMill integration are vast, achieving seamless connections requires careful planning and execution:
-
Identify Your Needs: Clearly define the goals of your integration. Are you aiming to streamline design-to-manufacturing workflow? Do you need to exchange data with existing software? Knowing your specific needs will guide your integration strategy.
-
Software Compatibility: Ensure compatibility between PowerMill and the software you intend to integrate with. Check for supported versions and file formats.
-
Data Management: Establish a clear data management strategy. Define how design data, toolpath information, and other relevant information will be transferred and stored between different software programs.
-
-
User Training: Provide adequate training for your team on the integrated workflows. This ensures everyone understands how to leverage the combined capabilities of PowerMill and other software effectively.
-
Testing and Validation: Thoroughly test the integration before deploying it in a production environment. This involves running simulations, validating data transfer accuracy, and ensuring smooth communication between all software components.
-
Ongoing Maintenance: Integration solutions may require ongoing maintenance. Stay updated on software updates, bug fixes, and potential compatibility issues that might arise with new software versions.
Advanced Integration Techniques: Embracing Automation
For manufacturers seeking to push the boundaries of efficiency, PowerMill offers advanced integration techniques that leverage automation:
-
Digital Twins: By creating digital twins of your CNC machines and tooling within CAM software, manufacturers can simulate the entire machining process virtually. Integrating PowerMill’s toolpaths with digital twin software allows for even more comprehensive process optimization. Potential bottlenecks or inefficiencies can be identified and addressed before production begins, leading to significant time and cost savings.
-
Cloud-Based Solutions: Cloud-based platforms are revolutionizing manufacturing data management and collaboration. PowerMill can integrate with cloud-based solutions to store and manage design data, toolpath libraries, and manufacturing workflows centrally. This enables real-time access to information from anywhere, fostering better collaboration between design, engineering, and production teams. Additionally, cloud-based solutions can facilitate integration with other cloud-based manufacturing applications, creating a truly interconnected ecosystem.
The Future of PowerMill Integration: A Connected Manufacturing Landscape
As the manufacturing landscape continues to evolve, PowerMill integration will play a critical role in achieving greater efficiency, agility, and responsiveness. Here’s a glimpse into the future:
-
The Rise of IIoT: The Industrial Internet of Things (IIoT) connects machines and devices on the shop floor, generating real-time data. PowerMill can integrate with IIoT platforms to receive real-time feedback on machine performance and adjust toolpaths dynamically based on sensor data. This allows for adaptive machining, where toolpaths can be optimized on the fly to account for factors like tool wear or variations in material properties.
-
AI-Powered Optimization: Artificial intelligence (AI) has the potential to revolutionize how manufacturers approach toolpath generation. PowerMill could integrate with AI algorithms that analyze design data, material properties, and machine capabilities to suggest optimal toolpaths automatically. This would significantly reduce programming time and allow for the exploration of a wider range of machining strategies, potentially leading to faster production times and improved part quality.
-
Standardized Integration Protocols: The development of standardized integration protocols would further streamline the process of connecting PowerMill with other software. This would allow for easier plug-and-play integration with a wider variety of manufacturing applications, reducing development time and costs associated with custom integrations.
In conclusion, PowerMill Ultimate’s ability to integrate seamlessly with various software programs empowers manufacturers to create a truly connected and optimized manufacturing environment. By strategically leveraging these integration capabilities, manufacturers can achieve significant improvements in efficiency, reduce costs, and gain a competitive edge in today’s dynamic market. As technology continues to evolve, PowerMill integration will undoubtedly play an even greater role in shaping the future of intelligent and adaptive manufacturing.
-