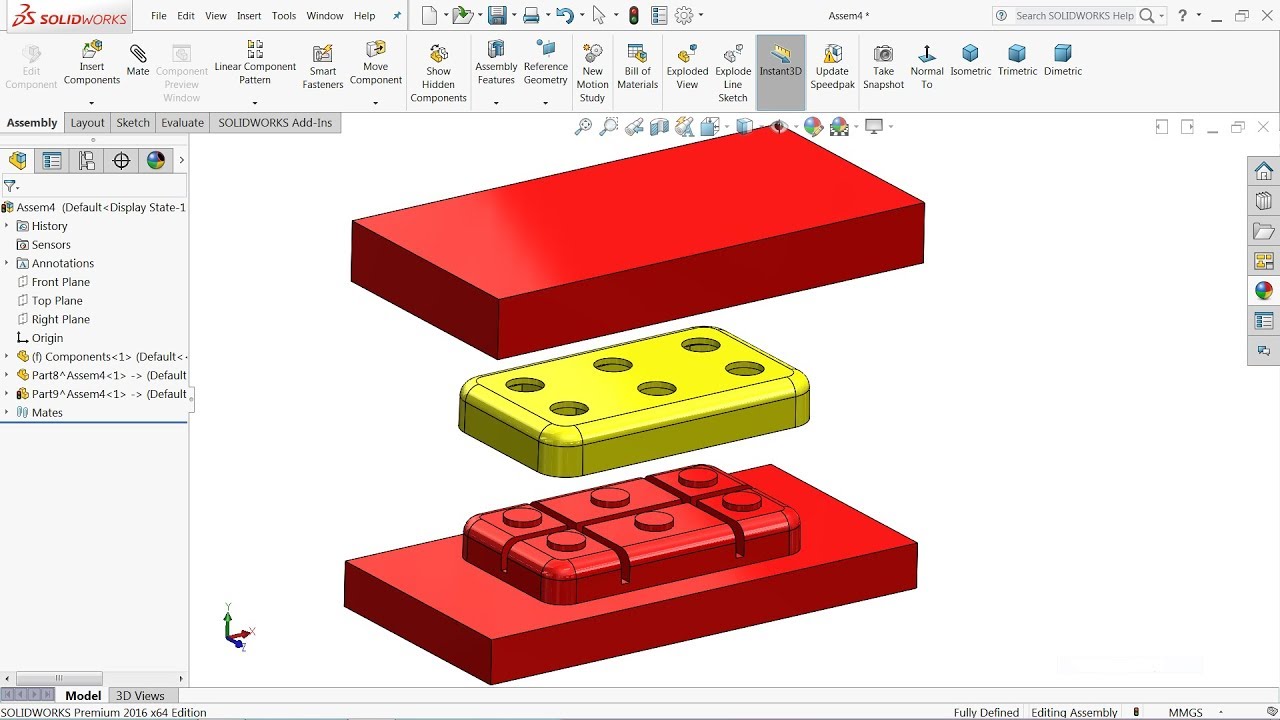
Mold design stands as a critical aspect within SolidWorks, offering designers and engineers a robust toolkit to create intricate molds for manufacturing plastic, metal, and composite parts with precision and efficiency. In this comprehensive guide, we embark on a journey through the complexities of mold design in SolidWorks, unraveling its functionalities, benefits, and practical applications across diverse manufacturing industries.
Understanding Mold Design:
Mold design in SolidWorks revolves around the creation and optimization of molds used in various manufacturing processes, including injection molding, blow molding, compression molding, and casting. These molds serve as precision tools for shaping raw materials into finished parts, components, and products with complex geometries and tight tolerances.
At its core, mold design encompasses the modeling of mold cavities, cores, inserts, cooling channels, and ejector systems, as well as the consideration of factors such as part geometry, material flow, shrinkage, and manufacturing constraints. By leveraging specialized tools and features, designers can create molds that optimize part quality, production efficiency, and cost-effectiveness.
Key Concepts of Mold Design in SolidWorks:
- Core and Cavity Design: SolidWorks provides a range of tools and features for modeling mold cores and cavities based on the geometry of the desired part. Designers can create precise representations of part features, including drafts, undercuts, ribs, and bosses, ensuring accurate replication in the final molded part.
- Parting Surfaces and Mold Splits: Mold design in SolidWorks involves defining parting surfaces and performing mold splits to separate the mold into core and cavity halves. Designers utilize tools such as parting lines, shut-off surfaces, and parting surfaces to create clean, well-defined mold parting lines that facilitate mold assembly and operation.
- Draft Analysis and Optimization: SolidWorks offers draft analysis tools that enable designers to evaluate and optimize part designs for moldability. By analyzing draft angles, wall thicknesses, and part geometry, designers can identify potential molding issues such as sink marks, warpage, and ejection problems and implement design changes to improve moldability and manufacturability.
- Runner and Gate Design: Mold design in SolidWorks involves modeling runner systems and gate locations to control material flow and distribution during the molding process. Designers can create runner layouts, gate types, and gate sizes based on part geometry, material properties, and molding requirements, optimizing designs for filling, packing, and cooling.
Benefits of Mold Design in SolidWorks:
- Design for Manufacturability: Mold design in SolidWorks enables designers to create molds optimized for manufacturing processes such as injection molding, blow molding, and casting. By considering factors such as part geometry, material flow, and moldability, designers can minimize molding defects, reduce cycle times, and improve part quality and consistency.
- Efficiency and Productivity: SolidWorks streamlines the mold design process and enhances productivity by providing a comprehensive set of tools and features tailored to mold design tasks. Designers can create molds rapidly, iterate on design concepts efficiently, and generate detailed mold layouts and drawings automatically, reducing time-to-market and enhancing competitiveness.
- Cost Reduction: Mold design in SolidWorks helps reduce manufacturing costs by optimizing mold designs for efficiency and material usage. By minimizing material waste, optimizing cooling channels, and reducing cycle times, designers can lower production costs, improve profitability, and gain a competitive edge in the market.
- Quality Assurance: SolidWorks ensures high levels of quality and precision in mold designs through parametric modeling and advanced analysis tools. Designers can simulate mold filling, packing, and cooling processes, predict molding defects, and validate mold designs before manufacturing, ensuring that molds meet stringent quality standards and performance requirements.
Practical Applications of Mold Design in SolidWorks:
- Injection Molding: Mold design in SolidWorks is widely used in injection molding for producing plastic parts and components for various industries, including automotive, consumer goods, electronics, and medical devices. Designers create molds with intricate features, complex geometries, and tight tolerances, ensuring precise replication of part designs in molded products.
- Blow Molding: Mold design in SolidWorks supports blow molding processes for manufacturing hollow plastic parts such as bottles, containers, and automotive components. Designers model molds with multiple cavities, complex shapes, and uniform wall thicknesses, optimizing designs for blow molding parameters such as parison thickness, stretch ratios, and cooling rates.
- Casting: Mold design in SolidWorks is employed in casting processes for producing metal parts and components with intricate details and fine surface finishes. Designers create molds for sand casting, investment casting, and die casting applications, ensuring that molds accommodate shrinkage, draft angles, and gating systems for efficient and cost-effective production.
- Prototyping and Tooling: Mold design in SolidWorks facilitates the creation of prototypes, tooling, and fixtures for manufacturing processes. Designers leverage mold designs to produce prototype parts for testing, validation, and iteration, as well as tooling and fixtures for molding, trimming, and assembly operations, accelerating the product development cycle and reducing time-to-market.
Conclusion:
Mold design in SolidWorks represents a cornerstone of modern manufacturing processes, enabling designers and engineers to create precision molds for producing parts and components with complex geometries and tight tolerances. By leveraging specialized tools and features, designers can optimize mold designs for efficiency, quality, and cost-effectiveness across a wide range of industries and applications. Whether used for injection molding, blow molding, casting, or prototyping, mold design in SolidWorks empowers users to master complexity, achieve excellence, and drive innovation in manufacturing.