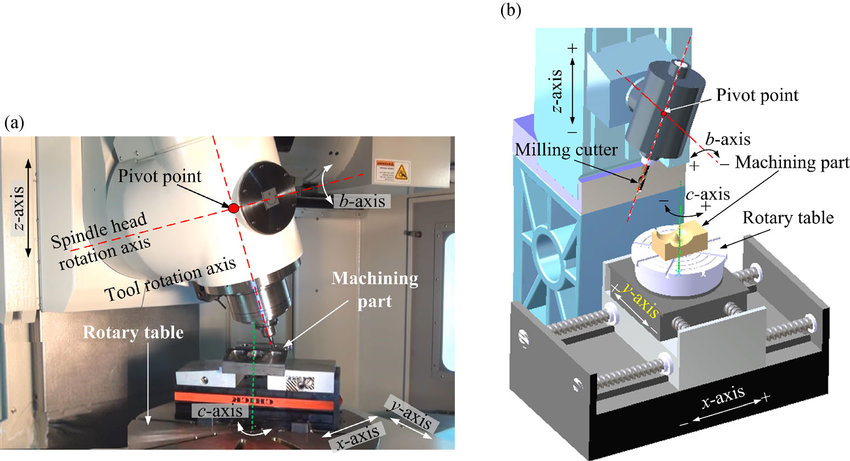
The symphony of a machine shop begins with the meticulous setup of its instruments – the machine tools themselves. Configuring these machines unlocks their full potential, ensuring precise operation, efficient production, and ultimately, high-quality parts. This comprehensive guide delves into the world of machine tool configuration, empowering you to become a maestro of this crucial art.
The Fundamentals: Building a Solid Foundation
Before embarking on advanced configurations, mastering the fundamentals is paramount. Here’s a breakdown of the essential steps involved:
-
Machine Installation and Leveling: Proper installation is critical for machine performance and safety. This involves carefully positioning the machine on a level and stable foundation, aligning the machine axes, and ensuring proper electrical and air supply connections.
-
Axis Alignment and Backlash Adjustment: Precise alignment of linear axes and minimization of backlash (looseness) in the mechanical components are crucial for achieving dimensional accuracy. Alignment procedures involve using precision tools like dial gauges and levels, while backlash adjustment might involve tightening specific components or utilizing pre-load mechanisms.
-
Spindle Orientation and Tool Change Mechanism: The spindle, the heart of the machine that rotates the cutting tool, needs to be accurately aligned and balanced. The tool change mechanism, responsible for automating tool exchange during machining operations, also requires proper configuration to ensure smooth and reliable tool changes.
-
Sensor Calibration: Various sensors monitor machine functions like tool presence, spindle speed, and coolant pressure. Calibration of these sensors ensures they provide accurate and reliable data to the CNC control system.
-
Setting Up Tooling and Workholding: Selecting the appropriate cutting tools and workholding devices is essential for each machining operation. The configuration process involves installing the tools in the tool holder assemblies, setting tool offsets (the distance between the tool tip and the machine reference point), and securely fixturing the workpiece on the machine table.
-
Defining CNC Control Parameters: The CNC control system relies on various parameters to execute machining programs. These parameters include spindle speeds, feed rates, coolant flow rates, and toolpath data. Accurate configuration of these parameters ensures the machine performs the machining operations according to the programmed specifications.
By meticulously following these fundamental setup procedures, you establish a solid foundation for successful machining operations.
Delving Deeper: Exploring Advanced Configuration Techniques
Once you’ve mastered the basics, the realm of advanced configuration techniques awaits. These techniques allow you to fine-tune the machine’s performance for specific applications and optimize overall machining efficiency:
-
Tool Offset Management: Advanced techniques involve utilizing tool wear monitoring systems and automatic tool offset correction to compensate for tool wear in real-time, ensuring consistent part dimensions and extending tool life.
-
Spindle Tuning and Thermal Management: Spindle performance is crucial for machining accuracy and surface finish. Advanced configuration techniques like thermal drift compensation and spindle balancing can help maintain optimal spindle performance throughout machining operations.
-
Adaptive Machining: This approach involves configuring the machine to adjust cutting parameters (spindle speed, feed rate) based on real-time sensor data, such as cutting forces or chip formation. This allows for dynamic optimization of the machining process for improved productivity and tool life.
-
Integration with Tool Management Systems: Modern CNC machines can integrate with dedicated tool management software. This allows for centralized tool data storage, automatic tool selection based on machining requirements, and streamlined tool lifecycle management practices.
-
Fixturing and Workholding Optimization: Advanced fixturing techniques, such as hydraulic clamping or vacuum fixtures, can improve workpiece security and repeatability. Additionally, utilizing work offsets and probing techniques allows for precise positioning of the workpiece relative to the machine axes.
By delving into these advanced configuration techniques, you can unlock new levels of precision, efficiency, and automation in your machining operations.
Understanding Your Machine: Tailoring Configurations to Specific Applications
The optimal configuration for a machine tool depends on the type of machining operation being performed and the material being machined. Here are some examples:
-
High-Speed Machining (HSM): HSM configurations prioritize high spindle speeds and rapid tool movements. This might involve utilizing lightweight tool holders, minimizing backlash in the machine axes, and optimizing cutting parameters for high feed rates.
-
Five-Axis Machining: Five-axis machining requires precise coordination of all five axes (X, Y, Z, A, B) to create complex 3D geometries. Configuring the machine for smooth and coordinated motion of all axes, incorporating collision detection and avoidance software, and utilizing appropriate toolpath generation strategies are crucial for successful five-axis machining.
-
Large-Scale Machining: For machining large workpieces, configurations prioritize machine stability and rigidity. This might involve utilizing extended tool lengths, employing specialized fixturing that distributes cutting forces evenly, and implementing tool wear monitoring strategies to ensure consistent part quality