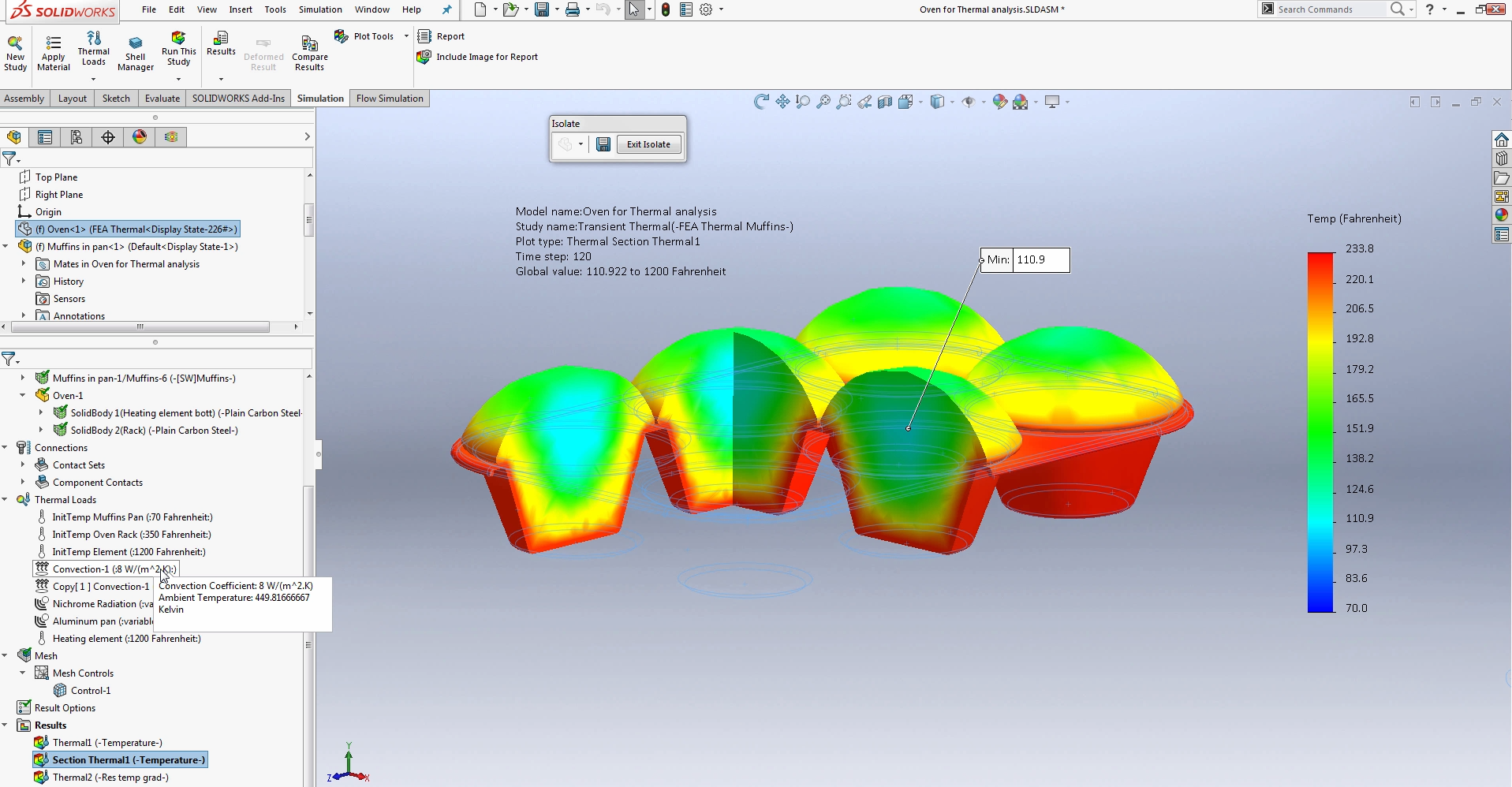
Introduction: SolidWorks Simulation offers a powerful set of tools for engineers and designers to analyze the thermal behavior of their designs. Thermal analysis is crucial for understanding how heat transfers within and between components, ensuring that designs meet performance requirements and remain within safe operating temperatures. In this comprehensive guide, we’ll explore the intricacies of performing thermal analysis in SolidWorks Simulation, covering everything from setting up simulations to interpreting results and optimizing designs.
Section 1: Understanding Thermal Analysis 1.1 Importance of Thermal Analysis: Thermal analysis plays a critical role in the design and optimization of mechanical systems, ensuring that components operate within acceptable temperature limits. Understanding how heat is generated, transferred, and dissipated within a design is essential for predicting performance, reliability, and longevity. SolidWorks Simulation provides engineers with the tools to simulate various thermal scenarios and evaluate the thermal behavior of their designs accurately.
1.2 Types of Thermal Analysis: SolidWorks Simulation offers several types of thermal analysis, each suited to different design scenarios and objectives:
- Steady-State Thermal Analysis: Analyzes the distribution of temperature within a design under steady-state conditions, where temperatures do not change with time.
- Transient Thermal Analysis: Analyzes how temperatures change over time in response to transient thermal loads, such as heating or cooling events.
- Convection and Radiation Analysis: Evaluates heat transfer through convection and radiation between surfaces and surrounding fluid or environments.
- Thermal Stress Analysis: Considers the thermal expansion and contraction of materials, leading to mechanical stresses and deformations.
Section 2: Setting up Thermal Simulations 2.1 Preparing the CAD Model: Start by importing your CAD model into SolidWorks Simulation or creating a new simulation study within SolidWorks. Ensure that the model geometry is complete and accurate, with appropriate material properties assigned to each component. Define any heat sources, boundary conditions, and thermal loads that will affect the thermal behavior of the design.
2.2 Defining Simulation Parameters: Configure the simulation settings in SolidWorks Simulation, specifying the type of thermal analysis (steady-state or transient), the thermal conductivity of materials, the initial and ambient temperatures, and other relevant parameters. Define the mesh settings to discretize the model geometry into smaller elements for numerical analysis, balancing mesh refinement with computational efficiency.
Section 3: Applying Thermal Loads and Boundary Conditions 3.1 Heat Sources and Sinks: Identify and define any heat sources or sinks within the model, such as electronic components, motors, or heating elements. Specify the power output or heat flux for each heat source, representing the rate at which heat is generated or absorbed within the design. Consider the distribution and intensity of heat sources to accurately capture their impact on the thermal behavior of the system.
3.2 Boundary Conditions: Define the boundary conditions that govern heat transfer at the surfaces of the model. Specify ambient temperatures, convection coefficients, and emissivity values for surfaces that interact with surrounding fluids or environments. Model heat transfer through convection by defining heat transfer coefficients and reference temperatures for fluid-solid interfaces. Account for radiation heat transfer by specifying emissivity values and environmental temperatures for radiating surfaces.
Section 4: Running Simulations and Analyzing Results 4.1 Running the Simulation: Once the simulation setup is complete, run the thermal analysis in SolidWorks Simulation to calculate temperature distributions within the model. Depending on the complexity of the model and the type of analysis, simulations may take varying amounts of time to complete. Monitor the progress of the simulation and check for convergence to ensure accurate results.
4.2 Interpreting Results: After the simulation is complete, analyze the results to gain insights into the thermal behavior of the design. Visualize temperature distributions using color maps, contour plots, or temperature gradients to identify areas of high temperature gradients or thermal stress concentrations. Evaluate heat fluxes, temperature gradients, and temperature profiles at critical locations within the model to assess thermal performance and compliance with design requirements.
Section 5: Optimizing Designs and Iterating 5.1 Design Optimization: Use the insights gained from thermal analysis to optimize the design for improved thermal performance. Identify areas of excessive heat generation or temperature rise and explore design modifications to mitigate thermal issues. Consider strategies such as adding heat sinks, improving ventilation, optimizing material selection, or redesigning component layouts to enhance thermal efficiency and reliability.
5.2 Iterative Analysis: Perform iterative thermal analysis in SolidWorks Simulation to assess the impact of design changes on thermal behavior. Modify the model geometry, boundary conditions, or material properties as needed, and rerun the simulation to evaluate the effectiveness of design modifications. Iterate through multiple design iterations, refining the design based on simulation results, until satisfactory thermal performance is achieved.
Conclusion: Thermal analysis is a critical aspect of engineering design, ensuring that designs meet performance requirements and remain within safe operating temperatures. With SolidWorks Simulation, engineers and designers have access to powerful tools for simulating and analyzing the thermal behavior of their designs accurately. By following the guidelines outlined in this comprehensive guide, engineers can leverage SolidWorks Simulation to perform thermal analysis effectively, optimize designs for improved thermal performance, and ensure the reliability and longevity of their products. With practice, experimentation, and continuous learning, engineers can master thermal analysis in SolidWorks Simulation and create innovative designs that excel in thermal management and performance.