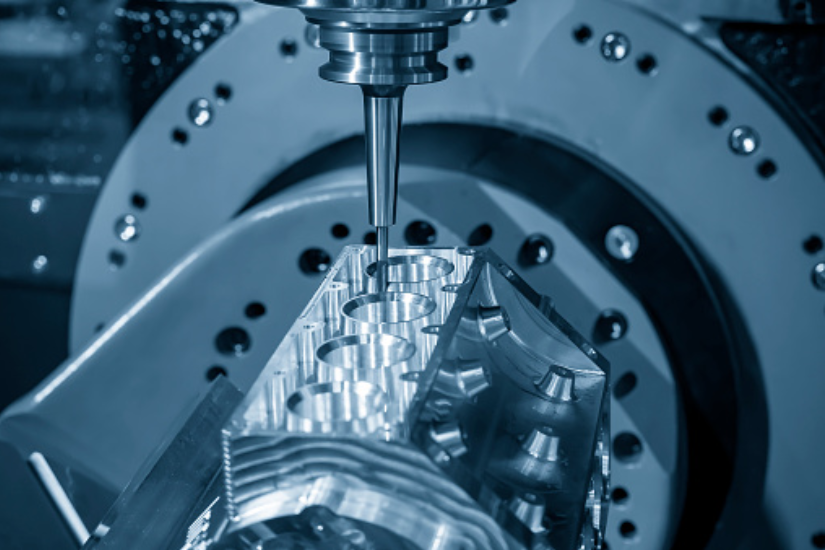
Understanding Machine Kinematics: The Foundation for Effective Programming
Multi-axis CNC machines offer a significant leap in machining capabilities compared to their 3-axis counterparts. However, this added complexity requires a deeper understanding of machine kinematics, the branch of mechanics that deals with the motion of rigid bodies. Here’s a breakdown of key concepts:
-
Machine Axes: Multi-axis machines typically have 4 or 5 axes, designated as X, Y, Z for linear motion and A, B, C for rotational motion around the respective linear axes. Understanding the range of motion and limitations of each axis is crucial for programming feasible toolpaths.
-
Work Envelope: The work envelope defines the maximum volume within which the tool center can reach while maintaining collision clearance with the machine structure. Programmers need to ensure all toolpaths stay within the defined work envelope to avoid collisions.
-
Tool Length Offset (TLO) and Work Offset (WO): These offsets account for the physical length of the cutting tool and the position of the workpiece within the machine coordinate system. Accurate definition of these offsets is essential for ensuring the programmed toolpath accurately reflects the desired machining operations.
-
Machine Datums: These are reference points on the machine used to establish the coordinate system for programming. Understanding the location and orientation of these datums is critical for accurately defining tool positions and orientations within the machine’s workspace.
Coordinate Systems and Transformations: Demystifying Tool Movement
Multi-axis machining involves complex tool movements that require precise control of both linear and rotational positions. Here’s how coordinate systems and transformations come into play:
-
Machine Coordinate System (MCS): This is the fixed reference system of the CNC machine. All programmed tool positions and orientations are defined relative to the MCS.
-
Tool Coordinate System (TCS): This is a user-defined coordinate system attached to the cutting tool. Programmers can define the TCS origin and orientation relative to the tool geometry to simplify toolpath programming.
-
Workpiece Coordinate System (WCS): This is another user-defined coordinate system that aligns with the features of the workpiece. Defining the WCS allows programmers to specify tool positions and orientations relative to the workpiece geometry.
-
Transformations: These mathematical operations convert positions and orientations defined in one coordinate system to another. Programmers utilize transformations to seamlessly move the tool between the MCS, TCS, and WCS as needed during the machining process.
Toolpath Generation Strategies for Multi-Axis Machining:
While traditional toolpath generation techniques used in 3-axis machining can be applied to some aspects of multi-axis machining, specific strategies are often employed to leverage the full capabilities of these machines. Here are some key approaches:
-
3+2 and 5-Axis Machining: These are the two most common multi-axis programming techniques. 3+2 machining involves using three linear axes (X, Y, Z) for primary machining and two rotary axes (typically A and C) for secondary positioning. 5-axis machining utilizes all five axes (X, Y, Z, A, B) simultaneously for complex toolpath generation.
-
Tool Center Point (TCP) Programming: This approach focuses on defining the desired path of the tool center point (TCP) in space. The CAM software calculates the necessary linear and rotary motions of the machine axes to achieve the desired TCP path.
-
Surface Toolpath Generation: For machining complex 3D surfaces, toolpaths are generated directly on the surface geometry. The CAM software calculates the required tool orientations and offsets to follow the surface contours accurately.
By understanding these core concepts and programming techniques, you can establish a solid foundation for creating effective toolpaths for multi-axis machining operations. In the next section, we’ll delve into advanced toolpath strategies, collision detection, and verification and simulation techniques to further refine your multi-axis programming skills.